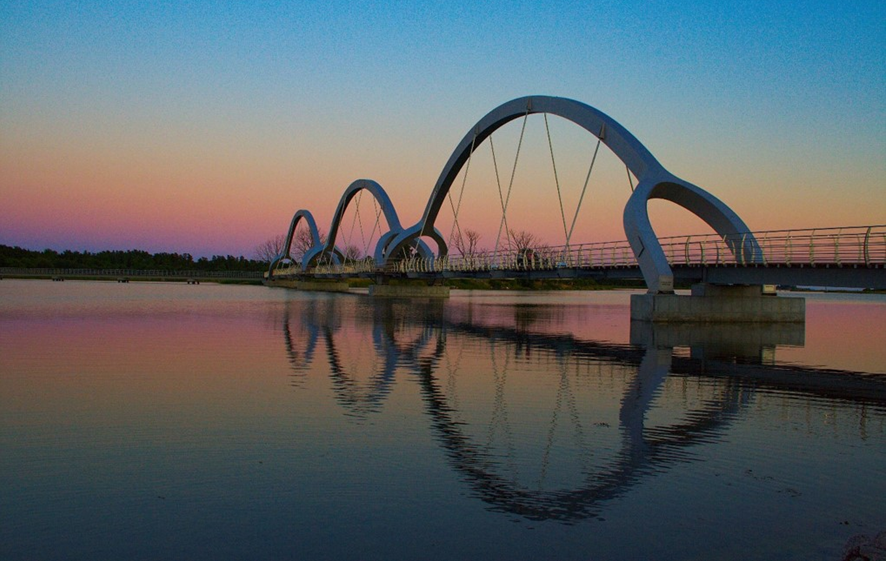
Steel industry
Swedish steel products have a low climate footprint in international terms and efficient, climate-smart steel products contribute towards lower material consumption, longer lifetimes, less wear and improved energy efficiency.
Carbon dioxide emissions from the Swedish iron and steel industry are approximately 6 Mtonnes/year. The highest proportion, approximately 85 percent, arises from the reduction of iron ore to form iron using coal. Other emissions come from the use of fuel for heating and heat treatment plus a smaller proportion from raw materials.
Targets in roadmap
2045: Fossil-free steel
To implement the roadmap, the industry is working on:
- Transitioning to reducing ore using hydrogen.
- Using bio-coal for some reduction and as an alloying element.
- Electrifying furnaces and using bio-based gas or hydrogen as fuel.
The Swedish Steel Producers’ Association, Jerkontoret, is coordinating the follow-up of the roadmap and has launched the climate research project Samforsk klimat. Its aim is to coordinate and support the research, innovation and development initiatives needed to implement the measures prioritised in the roadmap.
Progress since the roadmap was launched
Using hydrogen for iron ore reduction
Progress is being made in developing the new process technology to use hydrogen to reduce iron ore to iron. The pilot plant for producing sponge iron in Luleå started operation in 2020 and in parallel, preparations are being made to replace the blast furnace at SSAB in Oxelösund with an electric arc furnace to enable iron and waste reduced using hydrogen to be smelted in 2026. The first sponge iron has been further processed and in October, Volvo presented the world’s first vehicle made from fossil-free steel from HYBRIT’s pilot.
Interest in manufacturing steel using hydrogen has grown and in Boden, H2 Green Steel is planning a completely new steelworks.
Replacing fossil fuel with electrification and hydrogen
In recent years, several steel companies have electrified their heating and heat treatment furnaces. Ovako has successfully electrified five furnaces and has also run trials of hydrogen as a fuel.
Biocoal replacing fossil coal
Höganäs AB has successfully tested bio-coal, made via pyrolysis of biomass, as the alloying element and process reagent in the scrap smelting process. Bio-coal could also replace fossil coal in the process of reducing iron ore in powder manufacture. This would require bio-coal that is adapted to the processes in terms of durability and reactivity.
Industry challenges
Investments must be made in both new and existing technology coordinated with the companies’ investment cycles. More efficient permit processes are therefore crucial if measures to reduce emissions are to be implemented.
To achieve this, industry and government agencies need to work together for an effective process for sustainable growth.
Measures to cut emissions in iron and steel production are leading to an increased need for electricity of between 20 and 60 TWh. This makes great demands for higher production and transfer capacity in the electricity system and for this to be achieved cost-effectively with security of supply. The need for bio-based raw materials and fuels is also growing but uncertainty about future access risks slowing development.
Competition is tough on the global steel market but there are major differences in terms of climate requirements. Therefore, it is important that national and European regulations create a playing field that supports the companies’ opportunities to invest in new technology during the transitional period.
- Aggregates industry
- Agricultural sector
- Automotive industry – heavy transport
- Automotive industry – passenger cars
- Aviation Industry
- Cement industry
- Concrete industry
- Construction and civil engineering sector
- Digitalisation consultancy industry
- Electricity sector
- Fast moving consumer goods industry
- Food retail sector
- Forest sector
- Gas sector
- Heating sector
- Heavy road haulage industry
- Maritime industry
- Mining and minerals industry
- Petroleum and biofuel industry
- Recycling sector
- Ski resort sector
- Steel industry
Process owner: Jernkontoret
Published: 2018