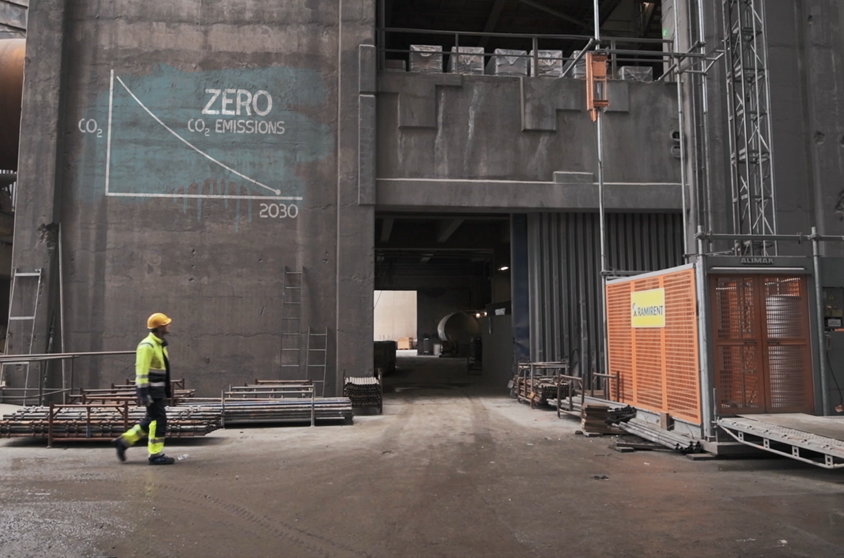
Cement industry
Cement is the key component in our most common construction material, concrete. Today, cement manufacture accounts for four percent of Sweden’s greenhouse gas emissions.
The key challenge for the cement industry is the carbon dioxide emissions that arise when the raw material limestone is turned into cement clinker at high temperatures. The first global steps are now being taken towards climate neutral cement production.
Targets in roadmap
2030: The world’s first climate-neutral cement plant Scope 1–3 to come on stream in Gotland where a carbon sink of more than 300,000 tonnes of carbon dioxide will also be created.
To implement the roadmap, the industry is working on:
- the transition from fossil energy to bioenergy.
- driving projects for CCS in Norway and Sweden with the aim of having the world’s first climate-neutral cement factory up and running in Slite in 2030.
- using raw materials sparingly and limiting new production by increasing efficient use of resources, recycling and re-use.
Cementa is working to implement the roadmap.
Progress since the roadmap was launched
Steps on the way to CCS and climate-neutral cement in the future
In June 2021, HeidelbergCement presented an initiative to make Cementa’s plant in Slite the first carbon-netural cement factory in the world with the potential to become a carbon sink. The world’s first CCS plant for the cement industry is already being built on an industrial scale in Norway with operation set to start in 2024. In Sweden a pilot study is underway for a facility in Slite where up to 1.8 million tonnes of carbon dioxide are to be captured annually from 2030. This will cut Sweden’s total emissions by three percent and also open up the opportunity of creating a carbon sink of more than 300,000 tonnes as a larger proportion of the fuel will be biobased.
Energy and material recovery of waste offers more benefits
The cement industry is taking over some of society’s waste management burden. Waste can be sent for energy recovery as fuel in cement manufacture, replacing carbon, and be recycled in that waste products replace some virgin raw material.
- Since 2018, the Slite plant, which accounts for 75 percent of Sweden’s cement production, has increased the proportion of recycled fuel by 10 percentage points from 59 percent to 69 percent. About a quarter comes from biomass. Work is underway to be able to use only bioenergy or electricity in the future.
- The use of waste materials is growing, and since 2019 the cement industry has replaced parts of the virgin raw material with approximately 200,000 tonnes of slag from the steel industry, reducing emissions by about 60,000 tonnes as less limestone needs to be used.
Industry challenges
Environmental permits are critical to the transition of the cement industry both in terms of access to raw materials and the industrial transition. The bottlenecks are long lead times, unpredictability and a lack of a holistic approach in decision-making processes. Long-term permits would enable the supply of cement in Sweden to be safeguarded.
The transition of the cement industry means a multi-million kronor investment in Gotland. Such an investment also requires a long-term approach from the authorities. The existing electricity system to and on the island is approaching the end of its life and an upgrade needs to take into account the capacity that will be needed for this industrial transition, and to be capable of functioning with the increasing expansion of renewable power. However, the lack of a robust electricity network and the trend towards rising electricity costs in southern Sweden risk putting the brakes on an urgent climate transition.
- Aggregates industry
- Agricultural sector
- Automotive industry – heavy transport
- Automotive industry – passenger cars
- Aviation Industry
- Cement industry
- Concrete industry
- Construction and civil engineering sector
- Digitalisation consultancy industry
- Electricity sector
- Fast moving consumer goods industry
- Food retail sector
- Forest sector
- Gas sector
- Heating sector
- Heavy road haulage industry
- Maritime industry
- Mining and minerals industry
- Petroleum and biofuel industry
- Recycling sector
- Ski resort sector
- Steel industry
Process owner: Cementa
Published: 2018