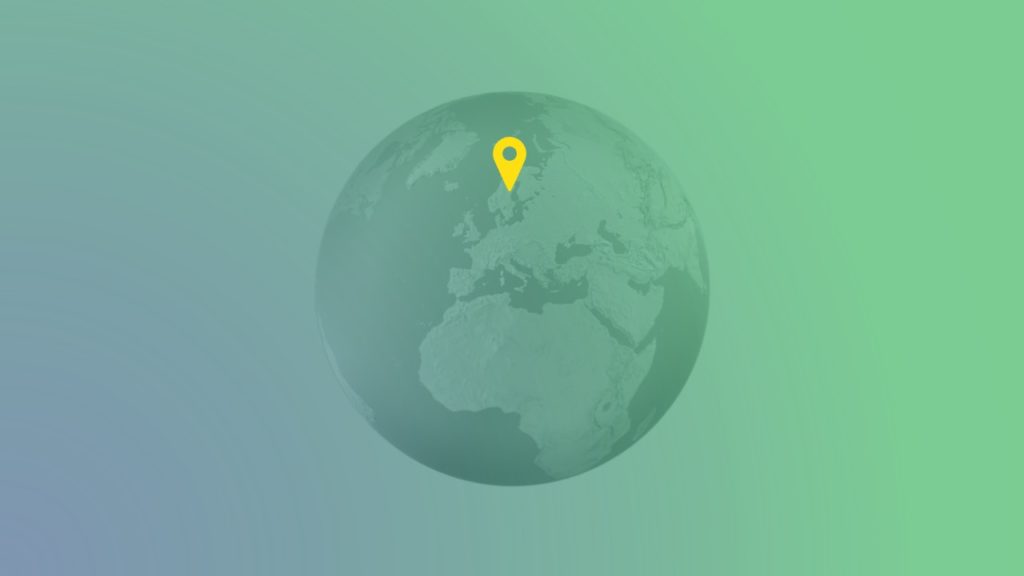
The journey to a fossil-free Sweden
Why should Sweden take a lead?
Export of solutions to benefit the climate and the economy
From climate policy to export policy
In the present-day world there are no possibilities of forcing other countries to reduce their emissions. So the best possibility that a small country has of influencing global emissions is to take a lead and export solutions and show, at the same time, that it is possible to combine a high standard of living with emission reductions.
The vision is for Sweden to be a permanent world exhibition for fossil free technology and climate-smart solutions. Sweden should be the country that companies and other countries go to when they want to buy or develop fossil free systems. This benefits the business sector and exports, which thereby contribute to enhancing well-being at home while contributing to emission reductions globally. By taking a lead and showing how this promotes the country’s own interests, we can also inspire others to follow suit.
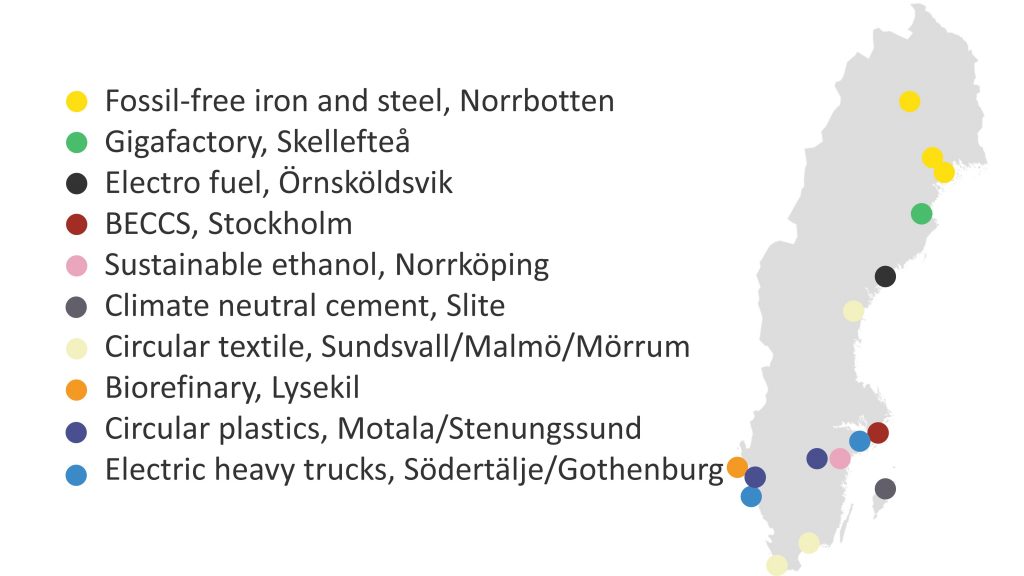
This strategy has meant that the climate issue in Sweden has therefore gone from being environment policy to having more to do with enterprise and export policy.
Some of the industrial projects that Sweden can showcase as part of that world exhibition are:
Cooperation between LKAB, SSAB and Vattenfall (HYBRIT) to transform the thousand years old coal based technology of steel making. By using hydrogen instead of coal, the process can revolutionise an industry that accounts for 6-7% of global greenhouse gas emissions.
A pilot facility is running in Luleå and the technology will be scaled up in Gällivare and fossil-free steel should be commercially available by 2026.
When fully implemented by SSAB this will reduce approximately 10 per cent of the total Swedish greenhouse gas emissions and the company aims to transform all its operations in Sweden and Finland by 2030.
By 2045 the goal for the mining company LKAB is to have gone from selling iron ore pellets to sponge iron produced with green hydrogen. This will make it possible for their customers all over the world to make fossil-free steel with the potential to lower total emissions with 30 million tonnes CO2e.
Read more about HYBRITHYBRIT is not the only project focusing on fossil-free steel. The new company H2 Green Steel is planning for steelproduction in Boden starting 2024 in collaboration with customers across multiple segments including automotive, commercial vehicle, white goods, furniture, and industrial equipment.
Read more about H2 Green SteelIn Skellefteå, one of Europe’s largest factory for electric car batteries started production in 2021. Northvolt has a strong focus on increasing the recycling efficiency of the batteries with the target of using 50 per cent recycled material in the batteries by 2030. In cooperation with Volvo Cars a new factory is planned in Gothenburg and is supposed to be ready for production start in 2025.
Read more about NorthvoltThe first commercial production site for electro methanol in Sweden. Carbon dioxide from the biofuel heat and power plant Hörneborgsverket is captured and together with green hydrogen used to produce electro methanol for the maritime industry.
The facility is a cooperation between Övik Energi and Liquid Wind and will produce 50 000 tonnes of methanol a year, starting 2024.
Read more about Liquid WindNegative emissions from district heating. Stockholm Exergi is one of the first companies in the world to be exploring large scale carbon capture and storage (CCS) from a biofuel heat and power plant. Carbon dioxide is to be captured, transported and buried below the ocean floor. A demonstration project is running and the goal is to implement it in full scale by 2025 capturing 800 000 tonnes of carbon dioxide a year.
Read more about Stockholm Exergi
In Norrköping, Lantmännen Agroetanol is producing ethanol from grain with carbon dioxide reduction of more than 90 per cent. And bio fuel is just one of the products that comes out of the process. The factory also produces for example green chemicals, protein and fibre, and carbonic acid for soda.
Read more about AgroetanolCementa in Slite, a part of Heidelberg Cement Group, aims to be the first climate-neutral cement plant in the world by 2030. The facility that currently accounts for 3 per cent of Sweden´s total emissions will use carbon capture and strorage technology (CCS) to capture 1,8 million tonnes of carbon dioxide a year for transport to a permanent storage site in bedrock,
Read more about CementaOnly five percent of textile on the Swedish market is recycled. Cotton farming consumes a lot of energy and water and have been difficult to recycle but new technologies are now scaling up.
Malmö: Siptex is the first large scale facility of its kind, sorting textile by colour and fiber using near-infra red light making it possible to manage large streams and produce textile fractions adapted for different recycling processes.
Read more about SiptexSundsvall: Renewcell, in partnership with e.g H&M, recycles cotton on an industrial scale. The world’s first commercial scale chemical recycling plant for cellulosic textiles commissioning planned in 2022 with a production capacity of 60 000 metric tonnes per year. In 2025 the capacity will have grown to 360 000 metric tonnes.
Read more about RenewcellMörrum: Södra has developed the first process in the world for recycling blends of cotton and polyester by using cellulose from wood.
Read more about OnceMore
Preem is converting their oil refinary in Lysekil to become the biggest producer of biofuel in Scandinavia. The facility will have the capacity to produce 650 000-950 000 cubic meters of biofuel a year reducing emissions through the value chain by 1,2-1,7 million tonnes ocf carbon dioxide. It is planned to be in operation by 2024 and the entire company aims to be climate neutral by 2035.
Read more about Preem’s transitionMotala: The biggest and most efficiant plant for plastic recycling in Europe is in Motala. Operating since 2019 it can sort 20 tonnes/hour. It will now be developed so that in 2023 it can handel all packages from Swedish household and be able to sort out and recycle twelve different types of plastic. Any small parts of plastic that remain after the sorting process are separated to be sent to chemical recycling, or to become new composite products.
Read more about Site ZeroStenungssund: With the mechanical recycling beeing used today only 15-20 per cent of the plastics can be recycled and after every loop the quality decreases. Now chemical company Borealis and recycling company Stena recycling has started a project for chemical recycling. Plastic waste streams of lower quality can then be recycled into high-quality base chemicals and thereby closing the loop, making it possible to use the recycled material in areas with high standards of security and purity.
If the initial project is succesful operations could start by 2024.
The target for 2030 in the automotive industry’s roadmap for heavy transport is for 50 per cent of all new trucks to be electric. Both Södertälje based Scania and the Gothenburg based Volvo Trucks have already put electric models with batteries on the market. They are also developing electrical vehicles with fuel cells that runs on hydrogen for long distance transports.
Besides the established companies the start-up Einride has developed the first fully electric, totally autonomous transport vehicle to operate on a public road in the world.